Understanding timelines is crucial for resolving delays or disputes successfully. At Precision, we specialize in forensic schedule analysis. This enables us to provide a thorough examination of project schedules. Our seasoned experts combine advanced analytical techniques with deep industry knowledge. They dissect schedules from inception to completion. Whether you face construction disputes, claims management, or project recovery, our forensic schedule analysis services offer the insights you need. Thus, trust Precision to illuminate your project timelines. We help you navigate the complexities of dispute resolution with clarity.
Forensic Delay Analysis Process
To identify and analyze delays effectively, Precision employs various methodologies. Each serves specific purposes and scenarios.
- Contract Review and Analysis
- Thorough Review of the Project’s Contemporaneous Records
- Schedule Review and Validation
- Methodology Selection
- Delay Analysis
- Causation Analysis
- Weather Days Delay Analysis
- Apportionment
Forensic Schedule Analysis Methodologies:
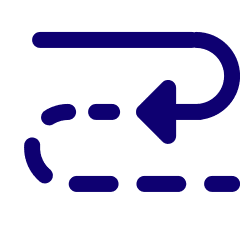
As-Planned vs. As-Built:
The as-planned vs. as-built observation technique is a crucial methodology in project management, especially within the construction industry. This approach thoroughly compares the original project schedule, referred to as the “as-planned” schedule, and the actual progress that has been recorded, known as the “as-built” schedule.
By identifying discrepancies between these two schedules, project managers can pinpoint delays, analyze their causes, and assess the overall effectiveness of project execution.
This technique facilitates a deeper understanding of project timelines and milestones and plays a vital role in managing stakeholder expectations. Project teams can implement timely corrective actions to mitigate risks. Thus, the project will be tracked by regularly monitoring the as-planned versus as-built comparison. This practice can help enhance stakeholder communication with valuable insights. It also provides transparency about project progress and ensures that any necessary adjustments can be made proactively. Ultimately, this comparative analysis serves as an essential tool for achieving project success and delivering results that align with initial expectations.
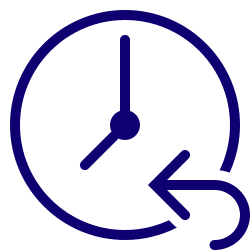
Forensic Time Impact Analysis (TIA):
Forensic Time Impact Analysis (TIA) is a comprehensive and structured methodology used to assess the effects of delays and disruptions on project schedules. This analytical approach involves a thorough examination of the original project plans, the actual progress made, and the specific impacts of any identified delays on the overall timeline. The primary goal of TIA is to determine the causal link between delays and their resultant impacts on project completion dates.
The process typically begins by establishing a baseline schedule, which serves as the foundation for comparison. Analysts then meticulously review project documentation, including change orders, daily logs, correspondence, and progress reports, to identify significant events that may have affected the project schedule. Using this information, TIA evaluates the sequence and timing of these events to ascertain their impact on project timelines.
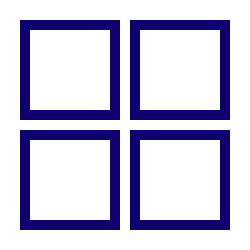
Window Analysis
Window analysis serves as an effective observational technique in project management by breaking down the overall project timeline into manageable segments, commonly referred to as “windows.” Each window signifies a specific timeframe wherein various activities and events transpire, thereby allowing for a detailed assessment of both progress and setbacks within that period.
This method not only provides a granular approach to identifying delays but also clarifies their impact on the overall project schedule. When project managers isolate different windows, they can closely analyze various factors contributing to delays within each segment, including resource allocation issues, scope changes, or unforeseen external influences.
Furthermore, Window Analysis elucidates the cause-and-effect relationships within the project. By examining the timeframe preceding a delay (the “before”) and its subsequent effect on the project schedule (the “after”), teams can accurately pinpoint specific issues and their moments of impact. This analysis not only aids in determining accountability for delays but also enhances future project planning and risk management by revealing patterns and recurring challenges.
In addition, Window Analysis fosters effective communication with stakeholders. This technique promotes transparency by presenting a clear visual representation of how timelines were affected during specific project phases. This builds trust and ensures that all parties comprehend the rationale behind any alterations to the anticipated completion date.
Overall, window analysis emerges as a powerful tool that enhances project monitoring and supports informed decision-making. Enabling a comprehensive understanding of both progress and setbacks ultimately contributes to more successful project execution throughout the lifecycle.
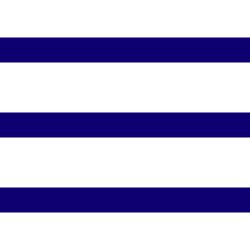
Collapsed As-Built Analysis:
Collapsed As-Built Analysis represents a targeted and analytical approach within project management, focusing specifically on adjusting the as-built schedule to reveal the completion date. By meticulously modifying this schedule, the technique effectively isolates delays solely attributable to the contractor, allowing for a clear perspective on the contractor’s performance without the influence of delays caused by other parties.
To implement this technique, project managers typically begin by identifying all delays and events recorded in the as-built schedule. Next, they remove or “collapse” the effects of external delays—such as issues stemming from clients, suppliers, or environmental factors—thereby streamlining the analysis to focus exclusively on the contractor’s responsibilities. As a result, this refined approach offers a more accurate reflection of the contractor’s impact on the project’s timeline.
Furthermore, a collapsed as-built analysis clarifies the contractor’s performance. It also enhances accountability by pinpointing specific delays linked to the contractor’s actions or inactions. As a powerful tool for evaluating construction schedules, it aids in dispute resolution and can provide valuable insights for negotiations or claims regarding the contractor’s performance.
Moreover, this analysis fosters improved future planning. By understanding the precise nature and scope of delays directly caused by the contractor, project managers can identify areas for improvement in resource management, scheduling practices, and risk assessment strategies. Consequently, teams can develop more effective mitigation plans, thereby increasing the likelihood of timely project completion in subsequent phases or projects.
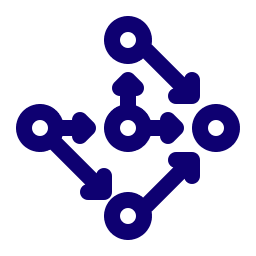
Forensic Critical Path Method (CPM) Analysis:
Forensic Critical Path Method (CPM) Analysis is a vital project management approach. Specifically targeting the critical activities within a project schedule. This analysis delves deep into the critical path—those tasks that directly impact the project’s completion time. Allowing project managers to evaluate how delays in these core activities ripple throughout the timeline.
By focusing on critical tasks, this method effectively highlights the link between specific delays and their broader implications for project completion. For example, if a critical activity suffers a setback, forensic CPM analysis helps teams understand the immediate delay and how it pushes back subsequent tasks. Ultimately affecting the project’s finish date.
Furthermore, this analysis enables project managers to prioritize resource allocation and implement effective mitigation strategies. By identifying which critical activities bear the most significant risk. Teams can proactively allocate additional resources or adjust schedules.
In addition, forensic CPM analysis provides a clear framework for communicating with stakeholders. By demonstrating how critical delays contribute to the project timeline, managers can effectively convey the importance of timely activity completion, fostering a heightened sense of urgency among team members.
In summary, a “construction delay forensic schedule analysis” is a detailed forensic analysis of a project’s construction schedules and project records. It identifies the critical drivers and causes of delays incurred by the project. The magnitude of each delay is calculated. The delay is then apportioned to the responsible party. Consequently, the Critical Path Method (CPM) has been used in the US for over 40 years. It identifies project delays through schedule analysis.
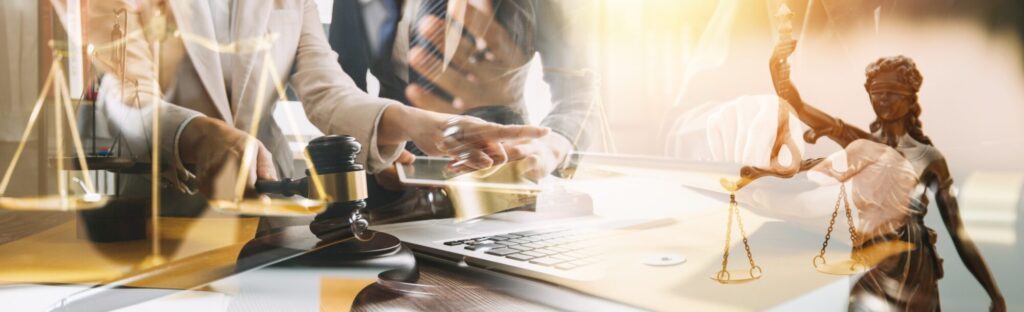
“… in the absence of compelling evidence of actual errors in the CPMs, we will let the parties ‘live or die’ by the CPM applicable to the relevant time frames.”
Santa Fe Inc. VABCA Nos. 1943, 1944 and 1946, 84-2 BCA. 17,340
Haney v. United States. United States Court of Claims. Mar 10, 1982. 676 F.2d 584
Forensic Scheduling Experts
Precision’s team of experts consists of seasoned construction professionals. They are well-versed in the various risks that companies encounter during the dispute resolution process. Navigating construction disputes can be complex. Whether it involves mediation, arbitration, or litigation support, Precision has the experience to provide guidance throughout the dispute resolution process. Additionally, with years of hands-on construction experience. Precision’s construction claims experts deliver a fair and reasonable assessment to effectively strengthen your case.